CORVEX CONNECTED WORKER
The Most Powerful Connected Workplace Platform for Manufacturing
Empowering manufacturing teams with real-time data insights and tools to drive performance & profitability
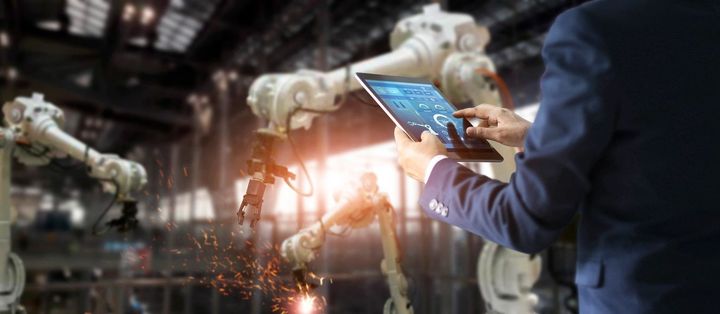
We Connect People, Assets And Data Across A Seamlessly Integrated Digital Platform
- Drive Operational Excellence & Transparency
- Supercharge Productivity & Efficiency
- Enable Process Standardization & Continuous Improvement
- Improve Asset Uptime and Performance
- Create a Proactive, Engaged & Collaborative Culture
Platform Tools
Daily Work Management
Tools to help teams standardize work and drive continuous improvement
Communication and Collaboration
Tools to drive teamwork and break down barriers across departments, shifts and locations
Health and Safety
Tools to support a positive safety culture, eliminate risk and improve compliance
Asset Reliability and Total Productive Maintenance
Tools and technology to digitally connect assets for improved uptime, reliability and performance
Learning and Skills Development
Tools to develop skills and share operational knowledge within your workforce
Why not put Best-in-Class enterprise technology in the hands of your workers?
Easy to Use and Intuitive Edge Computing that is Lightning Fast
Seamless IoT and Systems Integration
World-Class Security
Unlimited Languages
Enterprise Support
What Sets Us Apart?
At Corvex we do it differently and better. Here’s what makes us unique and why you should choose the Corvex Connected Workplace platform.
01
360-Degree Connectivity
We connect your workforce to their teams, the equipment that they use and the environment in which they work.
02
Unlimited Users
Each of our plans offer unlimited users. We don’t penalize you for adoption and engagement.
03
Real-Time
Data and Insights
Issues, insights and opportunities are captured and communicated across the platform instantly for fast action.
04
Manufacturing DNA
With deep knowledge and experience in digital transformation and within manufacturing, we are laser-focused on helping improve your business and bottom line.
05
Comprehensive and Configurable Features
We offer best-in-class integrated features and workflows that can be easily tailored to your operation – all within a single platform.
06
Quick & Easy Deployment and Adoption
Our platform was built for manufacturing teams with workers at the top of mind. Our tools are intuitive, easy to use and deliver value immediately.
07
Enterprise Scalability
We are a scalable enterprise platform that is proven to simply deliver whether your business operates at a global or a local scale.
The Corvex User Community and Testimonials
See what some of our customers are saying about how the Corvex Connected Workplace platform has helped them transform their business.
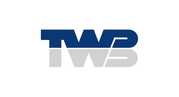
Providing real-time access to report out issues from the point of work has been a game changer and has driven significant results.
Amy Miller
Transformation Program Lead
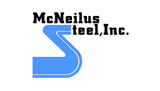
Digitizing the training process is an easy example of a significant win and quick returns with Corvex.
Zach Klemm
General Manager
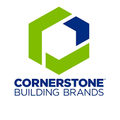
We realized a massive ROI through the incorporation of the Corvex into our operation and are seeing value on a daily basis.